
RCH Furnace Systems
RCH Associates furnaces are designed for optimum temperature accuracy and stability. Enclosed in a unitized, rugged and thermally insulated cabinet structure, up to 4 heating elements are packaged for easy maintenance and extended service life. Utilizing our proprietary ASTRA control system, RCH furnaces ensure maximum precision and ease-of-use for operators, with comprehensive automation and datalogging tools for process consistency. Most RCH diffusion and LPCVD processes are sold with guaranteed process performance criteria (within-wafer uniformity, wafer-to-wafer uniformity, etc). RCH has decades of experience producing a variety of custom furnace systems for various applications, including:
Click furnace type to see available processes
-
Dry oxidation
Dry oxidation with HCl enhancement
Dry oxidation with DCE enhancement
Wet Oxidation without hydrogen utilizing the RCH Steamer™
Pyrogenic oxidation, internal torch
Pyrogenic oxidation, external torch
Pyrogenic oxidation with HCl enhancement
Pyrogenic oxidation with DCE enhancement
DI:H2O bubbler oxidation
POCl3 phos dep liquid source doping
BBr3 boron dep liquid source doping
Solid source doping
H2 anneal/alloy
Forming gas anneal/alloy/sinter
Inert or noble gas anneal/alloy/sinter
-
Intrinsic polysilicon
Amorphous silicon
Phosphorous doped polysilicon
SiPOS (oxygen doped polysilicon)
Silicon nitride (Si3N4)
Low stress silicon nitride
Oxynitride
HTO
LTO
PSG
BPSG
TEOS
Doped TEOS
-
The Model VAF Furnace System is designed by RCH Associates to perform annealing, alloying or sintering of substrate films that are sensitive to residual oxidation such as refractory and composite metals.
The system includes a moving element that traveses the outside of the main vacuum process chamber.
This unique design allows for rapid heating and cooling of the process chamber while remaining under vacuum.
-
Bench Top Furnace for 50-150mm wafers
Bench Top Furnace for 150-200mm wafers
Stand-Alone Single or 2-Tube RCH Furnaces for 50-150mm wafers
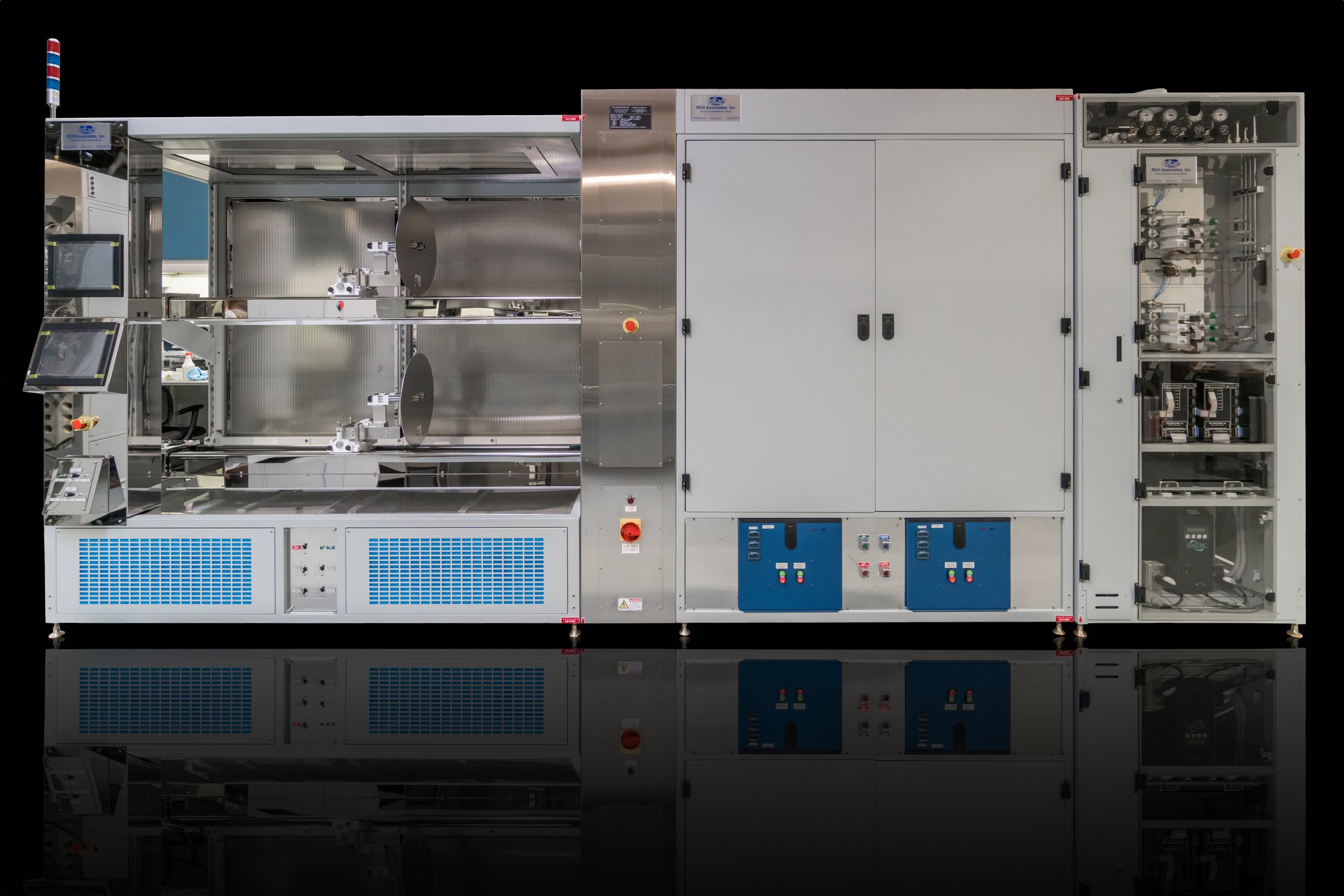
RCH Furnace Systems are designed around the following features:
(Click each section to expand details)
-
Unitized structural steel assembly
Hinged, locking and removable element access doors
Thermally insulated enclosure paneling
High temperature Urethane coating
Easy-to-adjust element alignment supports
Cabinet overtemperature interlock sensor
Leveling pads and optional seismic brackets
-
Stainless steel construction
Vents gases and heat from process tube or chamber
Indepently adjustable exhaust draw per tube-level
Cantilever closure or manual door sealing per tube-level
LPCVD flange and gas line fitting mounting scheme
Differential pressure gauge to monitor exhaust draw
-
Used to vent heated air from furnace cabinet top
HVAC control of furnace room
Water-cooled, high efficiency radiator
Air baffle paneling to direct air flow through cabinet
Exhaust fan module for air exhaust draw
-
Located within base of furnace cabinet
Encloses transformers, terminals and wire bussing
Encloses temperature controls and contactors/breakers
Easy accessibility to components
Pull down panels for easy access to control modules
EMO safety controls
Reduncant overtemperature interlock per element zone
-
Heating Elements
Options for temperature range anywhere from 350 to 1350ºC
+/- 0.5oC tolerance 600 to 1350oC range
+/- 1.0oC tolerance 350 to 600oC range
Vacuum formed high purity alumina insulation
Stainless steel shroud
Helical windings with captive spacing
Control and overtemperature TC spikes per zone
Enclosed TC wire channel
TC holding and alignment clips
Energy Kits
High purity alumina vestibule blocks
NEXTEL soft collars
Stainless steel capture rings, plates and collars
-
High efficiency digital SSR/SCR firing circuitry
Power control and circuit protection with EMO
CE-Compliant separation of control voltage and high power voltage
NEC-grade wiring
Easy accessibility to components
Main and control power disconnect contactors
Individual element power contactors and resets
Illuminated power indicators
Redundant overtemperature interlocks
208, 380, 415, 480VAC main power, 50 or 60Hz
4-Stack Horizontal LPVCD Furnace 200mm Wafers
3-Stack Vacuum Annealing Furnace 150mm Wafers
2-Stack Horizontal Diffusion Furnace 300mm Wafers